Our Mold Base Technology
In recent years, plastic parts have continued to get smaller, and the distance between pitches on narrow pitch connectors is now as small as 0.25 or 0.2mm. With the miniaturization of familiar digital products like home appliances, audio visual equipment and mobile phones, the internal parts are naturally getting smaller as well. The problem when manufacturing small plastic parts is the mold. Making ultra-small mold parts is very expensive and requires a high level of technology. These molds cannot be made just anywhere. Are these expensive, high-precision and difficult-to-obtain parts breaking on you regularly? Are the core pins wearing out and producing burrs when molding? Try our mold bases to reduce the cost of maintenance parts.
Are your core pins wearing out and producing burrs?
Core Pin A (Surface)
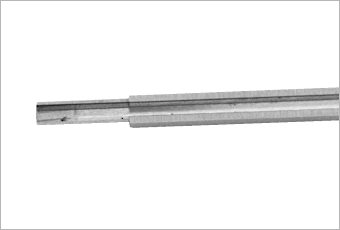
Marks left from electric discharge machining
Core Pin B (Surface)
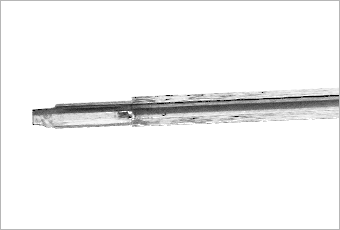
One-sided contact causing it to scrape against pin on other side and wear
As in the images above, the core pins wear out due to friction. There are several possible causes, but in the majority of cases if it is not tilting due to resin pressure or a dimensional failure then it is probably a mold mismatch.
The mold bases below are effective in reducing such defects.
Locating blocks such as the above are placed on the mold base. The second image is of a notch where a block is placed. This part fits as tightly as possible. Basically machining is done matching actual parts. It is placed 0-0.005mm from the reference plane. In the third image, the slippage in A and B is the same, and that of C and D is the same within an error of 0.005mm. The image is of a moving plate, but fixed plates are machined and placed the same way.
Pocket machining and positioning machining are performed using the same standard, and the same end mill is used for cutting. In order to ensure perpendicularity, end milling is performed with a specially ordered end mill with minimal back taper. Optionally, a guide pin can be press fitted, and a guide bushing can be attached. Positioning is left completely up to the block, and the guide pin is used only for guidance. Normally, GP and GB clearance is 0.015-0.025mm, so in the field of precision molds, guide pins do not serve a role in positioning. If there is one-sided contact, however, it will cause interference with the locating block. Accordingly, the GB set hole is given about 0.1mm of play. Place the locating block and attach GB, lining up the moving/fixed plates with GP press fitted. GB is attached with the positioning elements in place, thus eliminating GP/GB interference and locating block interference as much as possible.
Such strict positioning is of no use without the essential pocket precision. We have high-accuracy machining equipment. The dimensions will come out if the pocket is machined gradually for width, length and depth. However, if the machine is not accurate, perpendicularity and parallelism will never be achieved. Have you ever had the piece go in one side of the pocket but be tight on the other side? The mismatch doubles in rhomboid and trapezoid-shaped pockets when the moving and fixed plates are lined up. No matter how accurate the parts are, if the pocket is misaligned, it will not work. This is not a problem with accurate machining equipment. Our machining equipment is accurate within 0.4 micron over 100mm parallel and 0.5 micron over 100mm perpendicular. Without this kind of accuracy it is not possible to have an accurately positioned mold base. Try our highly recommended mold bases. You will not be disappointed!
Mold Base Equipment
ICAM has cutting-edge equipment to meet our customers’ needs.
Bridge-type machining center | Yamazaki Mazak -AJV32/605 (800 x 1500) x 2 -AJV32/405 (700 x 1000) x 7 |
---|---|
Vertical precision machining center | Mitsui Seiki Kogyo -VU50A (500 x 700) x 2 -VU65A (650 x 1280) x 1 |
Horizontal precision machining center | Mitsui Seiki Kogyo -FH630R (700 x 700) x 1 |
Flat-surface grinding machine | Okamoto Machinery: PSG-126B (600 x 1250) x 1 Nagase Integrex: PSG-64AN x 1 |
Wire electrical discharge machine | Fanuc
-α-1iB (500 x 400) x 1 Makino -W53FB x 1 |
Horizontal milling machine | OKK -MH-3P x 2 |
Vertical milling machine | OKK -MH-2V x 1 Okuma Howa -STM-2V x 1 |
Gun drill machine | Micro-machine
-KG-H800 (800L x 1000) x 1 |
Three dimensional tester | Mitsutoyo -CrysPlus4136M x 1 |
Jig milling machine | Shizuoka Machine Tool x 1 |
Radial drilling machine | Oya x 2 |
CAD/CAM | x 2 |
Band saw | 250.400 per machine |